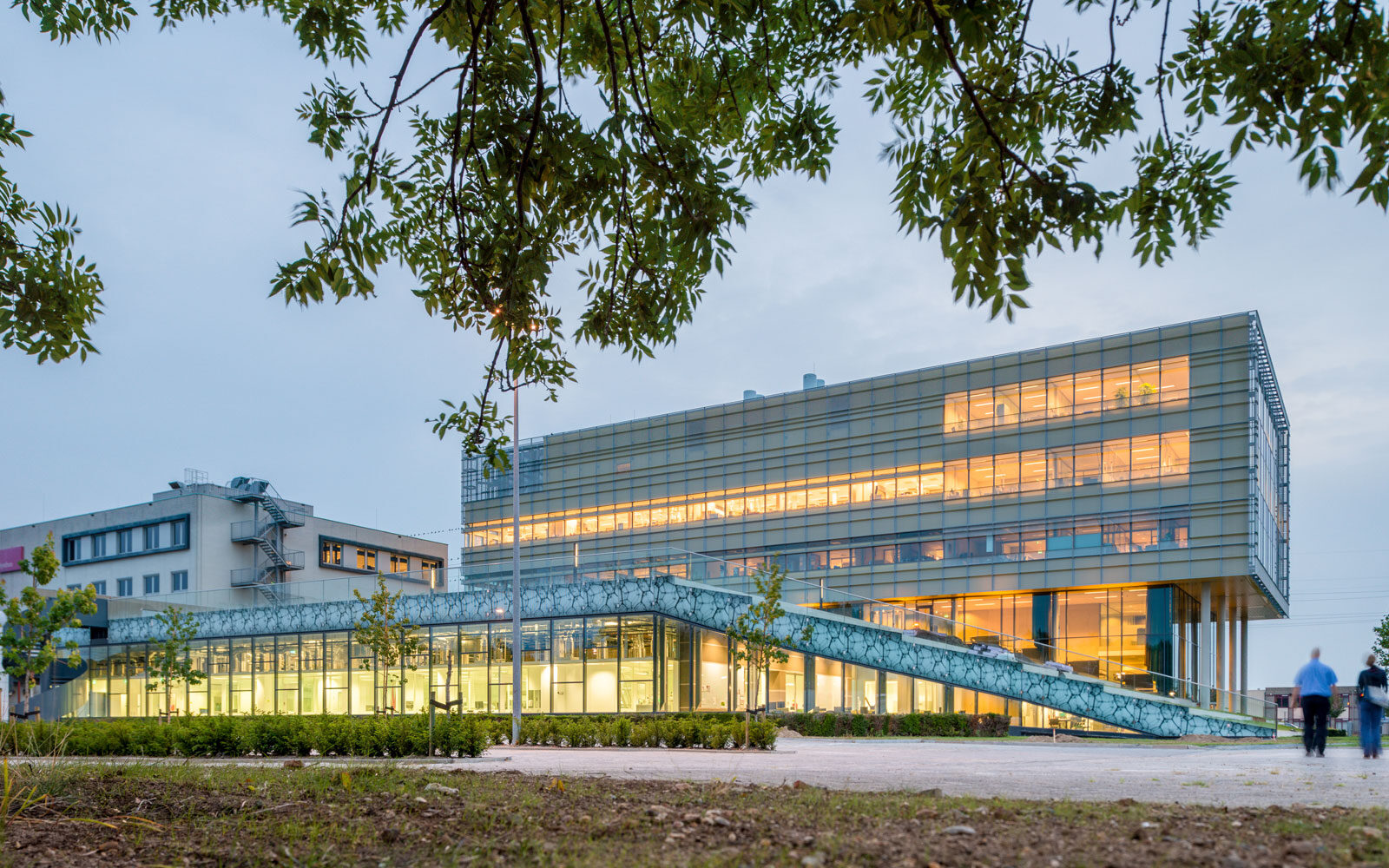
Byondis
Special biopharmaceutical testlab in green oasis
Byondis (previously Synthon BioPharmaceuticals), a pharmaceuticals company located in Nijmegen, is working on expanding its campus. The masterplan for this expansion was designed in 2008 by Broekbakema. The first of two new buildings on site are also of this architectural office. The testing factory was completed in 2015 for the production of monoclonal antibodies and is the third building in a series of seven. The sloping outdoor space that covers the factory is especially noticable; the campus is a green oasis in the grey concrete jungle of the industrial park of Nijmegen-West.
Testing factory
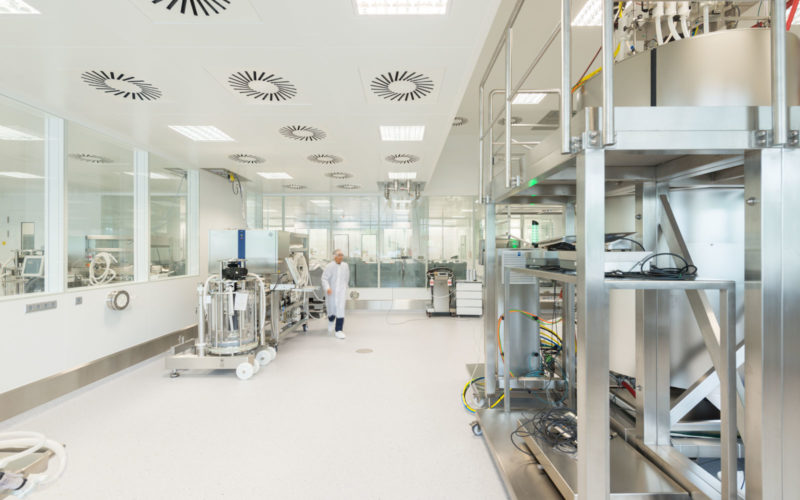
Architect Renze Evenhuis drew the mAb Plant together with colleague Jan van Iersel, a facility for the production of therapeutical monoclonal antibodies based on cell culture for usage in clinical studies. “Important work”, says Evenhuis: “Byondis uses the mAbs for their ADC-medicines. ADC, or anti-body drug conjugates, is the official name for the so-called “Trojan Horse” method in which a therapeutical antibody (protein) is recognized by specific receptors on tumor cells. A cytostat -a very poisonous chemical- is attached to this protein, which turns non-toxic when atached to it. The unique element of Byondis’ new ADC technology is that the poison is only released and effective once it enters the tumor cell and goes through a chemical process. An important development in the treatment of cancer.”
Raised landscape
The campus is situated at an industrial park where regular and unrecongnizable boxes are dime a dozen. “Broekbakema wants to change the Dutch industrial park with this masterplan”, says Evenhuis. “We started off with a green landscape where it is pleasant to be for all employees. Byondis wants to offer its employees an environment where they can work happily with enough space for meeting and relaxing. That’s why we raised the landscape, creating variantion, views and experiences.”
The new mAb Plant fits the terrain especially: the landscape rises up and continues as a green roof over the building. The side facades are of glass, creating a large and open building from which the employees have an overview of their surroundings. “This was possible because the three adjacent buildings have one public entrance. In terms of design and arrangement the three buildings are differen, but the materialization flows from one part of the building to the other. This creates a logical whole visually.”
Art
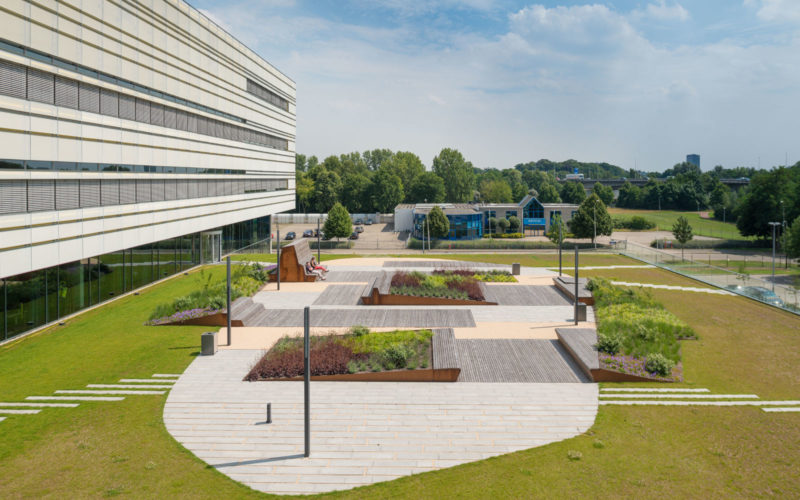
In the test factory everything is in one level. Above the working floor is a walkable ceiling allowing access to the services of the cleanrooms. “The big advantage is that the workflow in the cleanrooms is never disturbed, even if tehcnical maintenance is needed.” The architect chose to keep services visible from outside. “These services are the hart of this factory; and this should be seen, I think. And by leaving it in sigh, it turns into an element of art.”
Separated functions
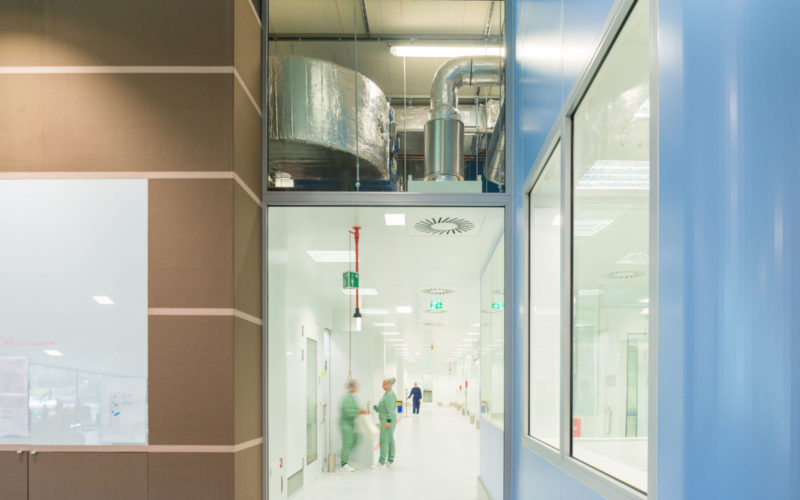
The sloping roof turns into a flat roof halfway. Also internally, this bend is a breaking point: the offices are located until here. On the bend are the dressing rooms and the airlock to the cleanrooms. The cleanrooms then start under the flat roof.
Also in the materialization the offices and cleanrooms are separated clearly. While soft and warm materials dominate the offices -wood, limestone, cabinets covered in felt- the cleanrooms are hard and sterile. “A deliberate choice”, says the architect. “Everything is made of glass and steel. The smallest of pollution is a risk to the workflow, meaning that it has to be visible and easily cleaned. The builder had to get used to the fact that we intervened with the cleanrooms. Normally this is a sort of dark spot in the design, as other parties envelop the cleanrooms in a package. We made it especially part of the design.”
Linear
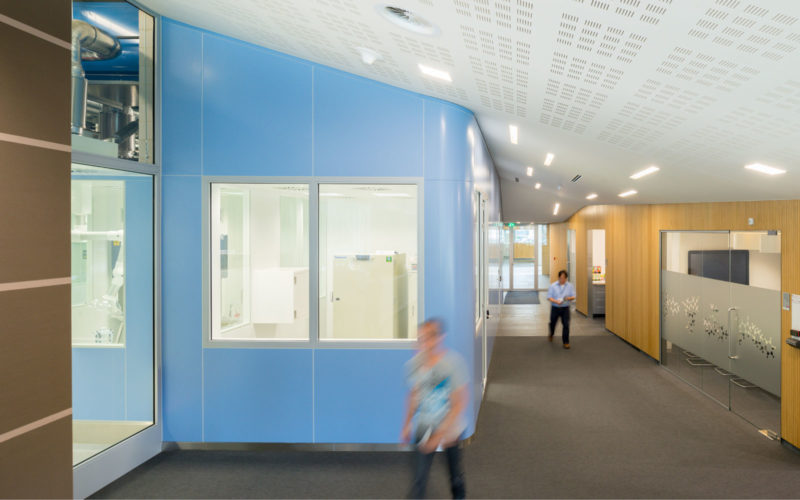
It is not without reason that Broekbakema makes its cleanrooms part of its design: the office has much experience in the design and setup of such spaces. “We are able to think together with our clients in designing the primary process in the most efficient way.” At Byondis this led to a special proposition: organize the production process linearly instead of circularly. “At Byondis we saw a linear process: all subsequent steps were placed in sequence. Normally the area of cleanrooms are laid out in a circular fashion, creating a closed-off block. By organizing the process linearly, the logistics improve greatly. Additionally, it became possible to place a raised hallway all along the length of the plant. This allows for views both inward and outward, creating visual relationships with the work that is the essence of the building. It additionally acts as a climatic buffer for the cleanrooms.”
This was a building is designed that arranges a complex workflow clearly and attractively. “The mAb Plant is transparent and improves the involvement and interaction between employees. Byondis tells the world outside: we have nothing to hide and our proud of our revolutionary work. And that is a revolutionarily different approach compared to the hidden location that cleanrooms often have.”
Maximum output
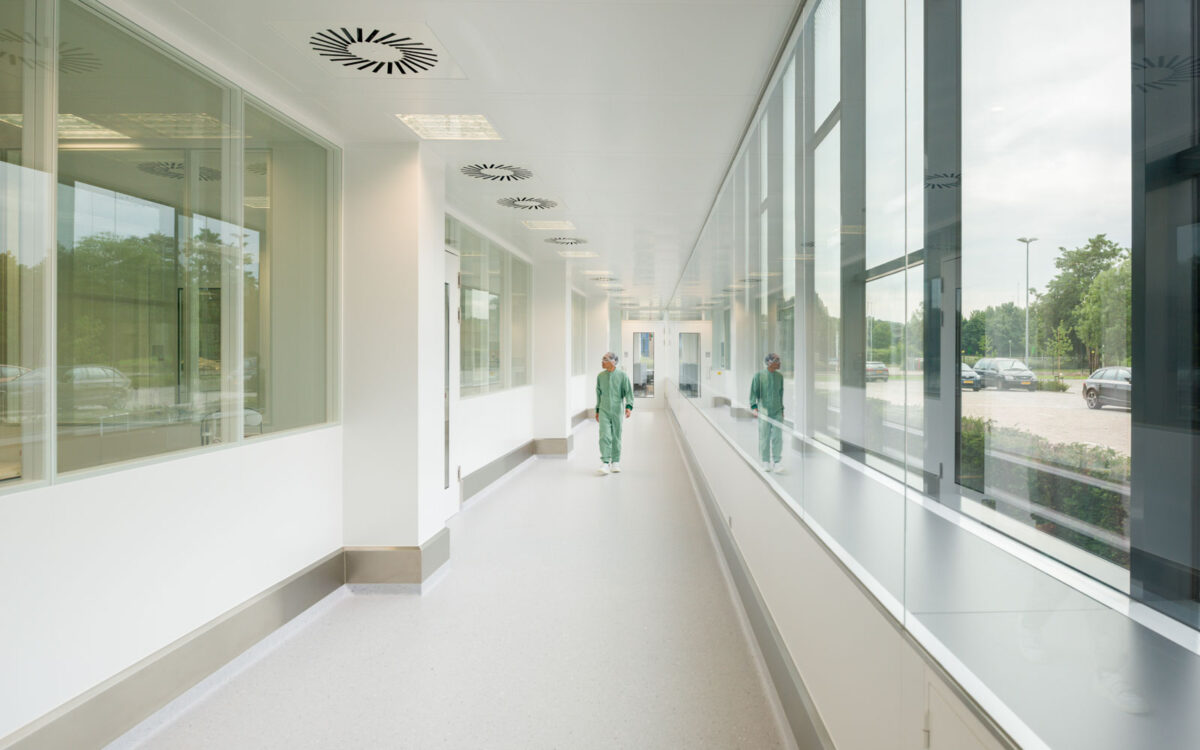
For Byondis this campus is also a search to the ideal way of structuring processes. It is a new form of research, where Byondis was not able to formulate all conditions and requirements either. “We were therefore involved from the start”, says Evenuis. “Within preset boundaries we try to get maximum output. Deadlines and budgeting are set, but within that we work optimally together in a Building Information Model (BIM). This allows for solutions to be processed efficiently, and are we able to cater to all of Byondis’ needs within a limited space. Excellent, because we were able to utilize our expertise in cleanroom and laboratory design to the fullest.”
This way the mAb Plant is, besides being refined, especially a statement of the highest order within the building ensemble.
- Images
- Menno Emmink Fotografie
We are happy to tell you more.
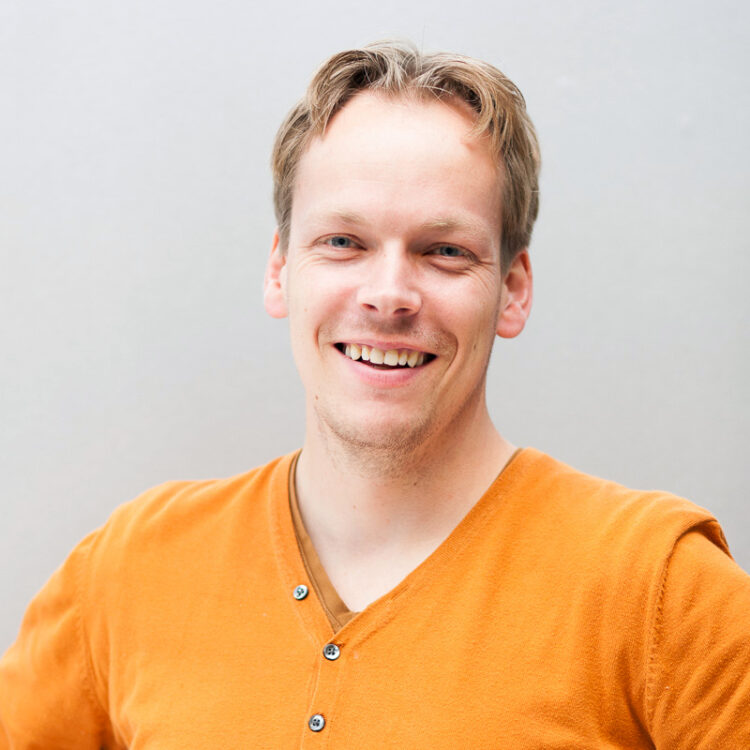
- ir. Renze Evenhuis
- Architect director